Plus de 24 milliards de paires de chaussures fabriquées chaque année. Elles sont l’outil principal de la majorité des activités sportives. On les lace à longueur de séances sans se douter des étapes en cascade nécessaires à l’étude de leur amorti, de leur résistance ou de leur ajustement au pied. Comment conçoit-on une basket, combien de temps faut-il pour la fabriquer, quelles sont les normes ? Les réponses auprès d’experts-nés et d’une marque française pas comme les autres. Reportage en immersion.
Par Léa Borie, Extrait de Women Sports magazine n°30 octobre-novembre-décembre 2023
Ça sent la colle, le cuir fraîchement découpé. Les machines s’activent avec une immense précision. Christophe Cumin, responsable du département chaussure au CTC (Comité professionnel de développement économique) à Lyon, nous ouvre la porte du laboratoire. Il est accompagné de Bénédicte Vermerie, directrice information et communication. On se sent un peu privilégié : les visites extérieures sont limitées, peu ont cette chance, alors il nous faut ouvrir grand les yeux.
Pourquoi avoir frappé à la porte du CTC ?
Parce que cet institut technologique de référence adopte une démarche scientifique d’accompagnement des entreprises pour promouvoir les progrès techniques. Ici, les projets sont initiés par les industriels ; le CTC vient en éclaireur. Il entend favoriser l’innovation en entreprise et faire émerger de nouvelles entités dans la filière.
Ce comité professionnel, financé en partie par une taxe fiscale, offre à ses membres à l’échelle nationale différents services : recherche et développement, veille, normalisation, savoir-faire, création, formation, subventions… C’est aussi une plateforme de mise en relation avec des ateliers français.
On y développe également un simulateur mécanique de marche et de course à pied pour mieux mesurer l’amorti notamment. Une vision globale pour les entreprises qui lancent un produit, quelle que soit la taille de leur structure, que ce soit Babolat, Millet, Salomon ou des marques naissantes comme Wizwedge. CTC s’exporte. Quatre sites ont été implantés en Asie pour se rapprocher des zones de production. Ils proposer majoritairement des prestations de contrôle qualité.
La conception d’une basket pour les nuls (ou les curieux !)
La normalisation
La vente de chaussures de sport françaises doit respecter des normes CE (REACH / innocuité) – absence de produits chimiques dangereux. Hormis ces interdictions, le champ est libre. Ce sont aux marques de fixer leurs propres règles. D’où l’intérêt de bien choisir son modèle. Pour être dite de fabrication française, la réglementation impose que la mise en forme de la tige et la fixation de la semelle soient faites dans l’hexagone
Les formations du CTC
Sont dispensées des formations aux entreprises pour expliquer la fabrication, l’industrialisation, les machines utiles afin d’apprendre à suivre une production… « Cela développe de la crédibilité auprès du fabricant, et permet de parler le même langage lors des collaborations CTC/marque, détaille Christophe Cumin, responsable du pôle chaussure. Salomon a par exemple suivi une formation pour tout son personnel footwear. Idem pour Babolat lorsque l’entreprise s’est lancée dans la fabrication de chaussures de tennis. Les écoles se rendent aussi au laboratoire ».
De l’industrialisation à l’usine
La confection Design, validation du concept, prototype, production… les étapes sont nombreuses ! Christophe Cumin nous explique qu’une fois que la marque a trouvé un financeur, elle se lance concrètement avec le design, le développement technique du concept, la réalisation de prototype, la validation du concept, l’essai joueurs, la fabrication de toutes les semelles dans toutes les pointures et enfin l’expédition.
Ce qui regroupe une dizaine de métiers au CTC, de la conception à l’essai en laboratoire en passant par la biomécanique. Fabriquer une paire de chaussures, c’est de 40 minutes pour un modèle simple à 120 minutes pour un plus complexe. En usine, cela représente entre 50 et 140 opérations, réalisées par une cinquantaine de personnes.
Le coût de production
Christophe prend une feuille de papier et prend le temps de nous expliquer les différences de coûts entre une fabrication française et asiatique, des salaires aux composants. Après bilan de son bref calcul, Christophe tranche : « Une paire de chaussure fabriquée en Chine et vendue 85 € devrait être vendue 197 € si elle était fabriquée en France, ce qui est difficile à envisager sans changer les pratiques commerciales. »
Ce qui explique un écart vertigineux dans les chiffres de fabrication de chaussures annuelles, qui tombent à 14 millions en France, sur les 24 milliards de paires fabriquées chaque année. Le plus gros marché est détenu haut la main par la Chine, avec 14 milliards, puis l’Inde avec 2,5 milliards, Vietnam et Indonésie en fabriquent 1 milliard.
Le savoir-faire
Hormis le coût, les capacités manquent sur notre continent, que ce soit en matière de main d’œuvre ou de machines. En France, depuis les années 70/80 et l’avènement du bac général contre les filières plus manuelles dévalorisées, les savoir-faire ne sont plus sur le territoire. « Il y a très peu de fabricants aujourd’hui, commente Bénédicte Vermerie. Il est aussi devenu difficile de recruter. Les marques font appel à des sous-traitants souvent basés hors de France ».
Christophe Cumin explique qu’ailleurs en Europe, certains ont su conserver leur entité propre et de l’entraide entre entreprises, ce qui n’a pas toujours été le cas en France : « Il faut se tourner vers l’Espagne, l’Italie et le Portugal. Mais ces entreprises ne sont pas assez importantes pour une production en grande quantité. De plus, certaines étapes ne seront possibles qu’en Asie, comme la semelle de running, qu’on ne sait pas faire en Europe. »
Visite d’un laboratoire d’un nouveau genre
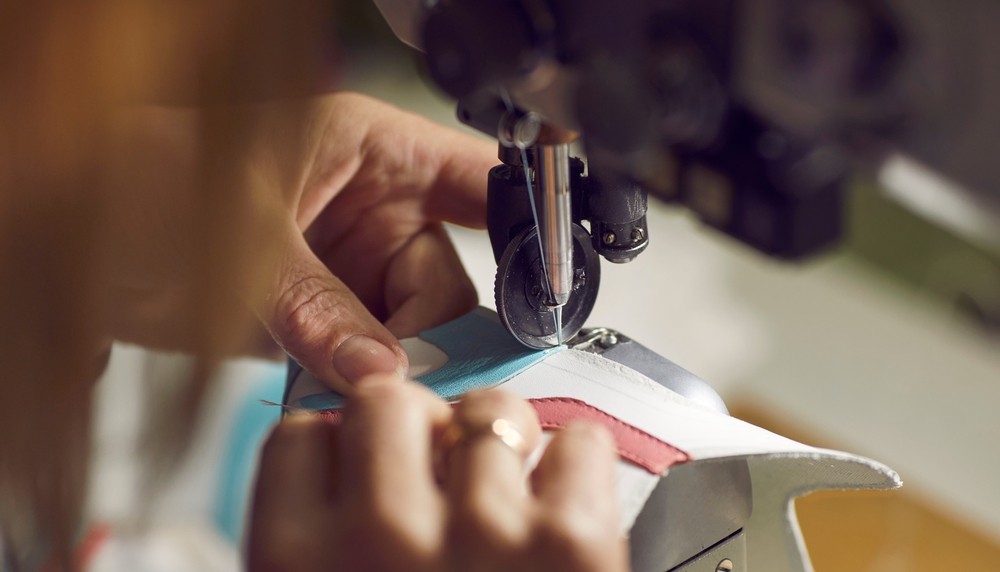
› Formier et machine 3D
Cette première étape incombe au formier ou last maker, un métier qui se perd. On rencontre l’artisan dans les couloirs, qui se joint à nous pour nous raconter son travail. La fabrication de la forme se fait avec une rappe en bois, une méthode de sculpture ancestrale !
Un scanner va sortir une image 3D du pied, le pied moyen français avec sa largeur moyenne. (Cette mesure peut être faite sur mesure si la chaussure est réalisée pour un athlète en particulier.) Cela passe par un logiciel de CAO pour dessiner en 3D. En ressort une forme en plastique, pour le patronage.
› Patronage du modèle
On vient ensuite créer la coquille moulée autour de cette forme, en accord avec le designer, le styliste. Il faut suffisamment de formes pour lancer la production dans toutes les tailles…
› Coupe et découpe
On passe sur la table de découpe numérique, adéquate pour toutes les matières en petites quantités. [4] On peut avoir jusqu’à 70 pièces pour les chaussures de randonnée montantes.
› Piquage sur la tige
Ce travail se fait à partir d’une machine à coudre bien spéciale, avec un pilier pour la tige, qui coud dessus-dessous. Cette étape de découpe / piquage comprend à elle toute seule 40 minutes de travail. Cela demande du doigté pour tendre la tige sur la forme juste ce qu’il faut. C’est bien l’opérateur qui fait la qualité du produit final.
› Mise en volume / montage
La mise en volume et la fixation de la semelle viennent terminer la chaîne.
Pour que la colle pénètre dans le cuir, il arrive de faire du cardage – poncer légèrement la peau, abraser le cuir – pour permettre un bon collage de la tige sur la semelle.
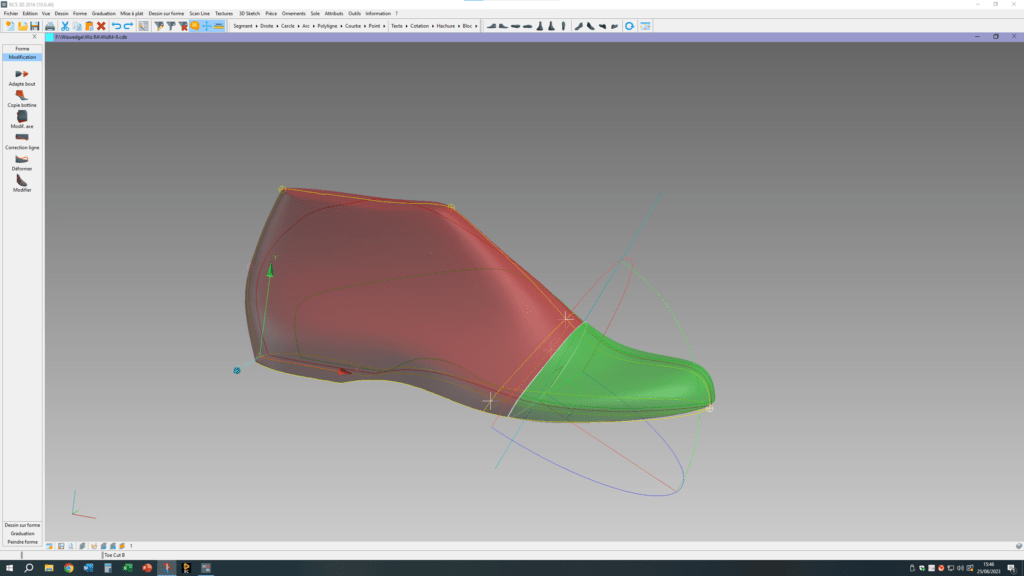
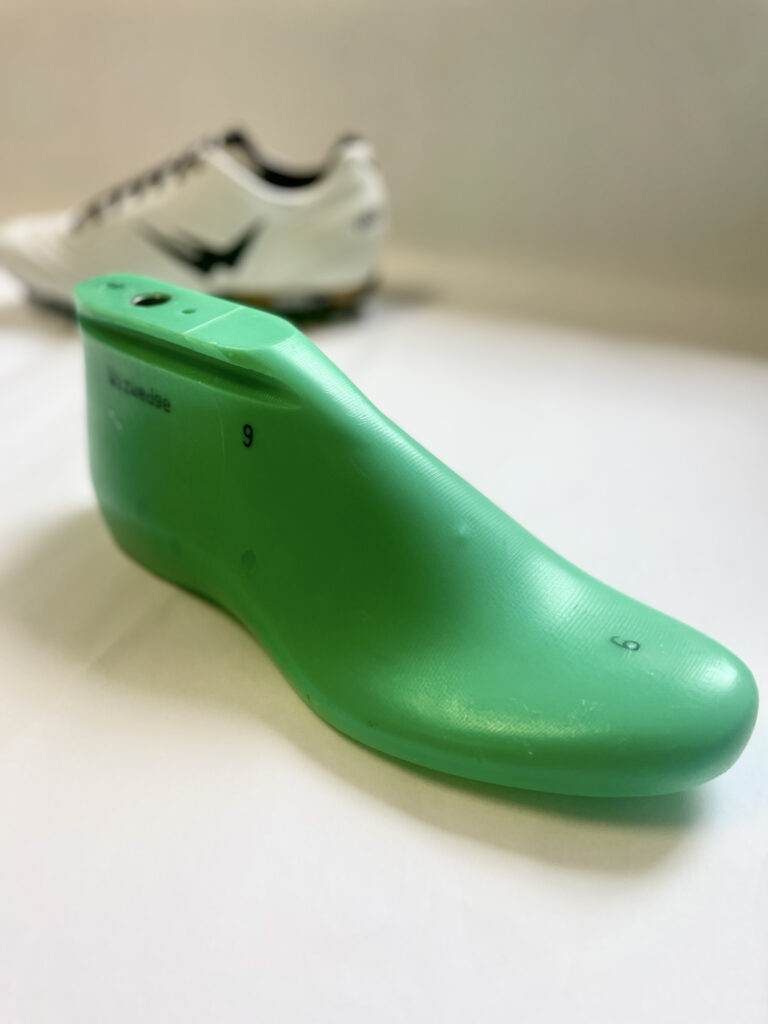
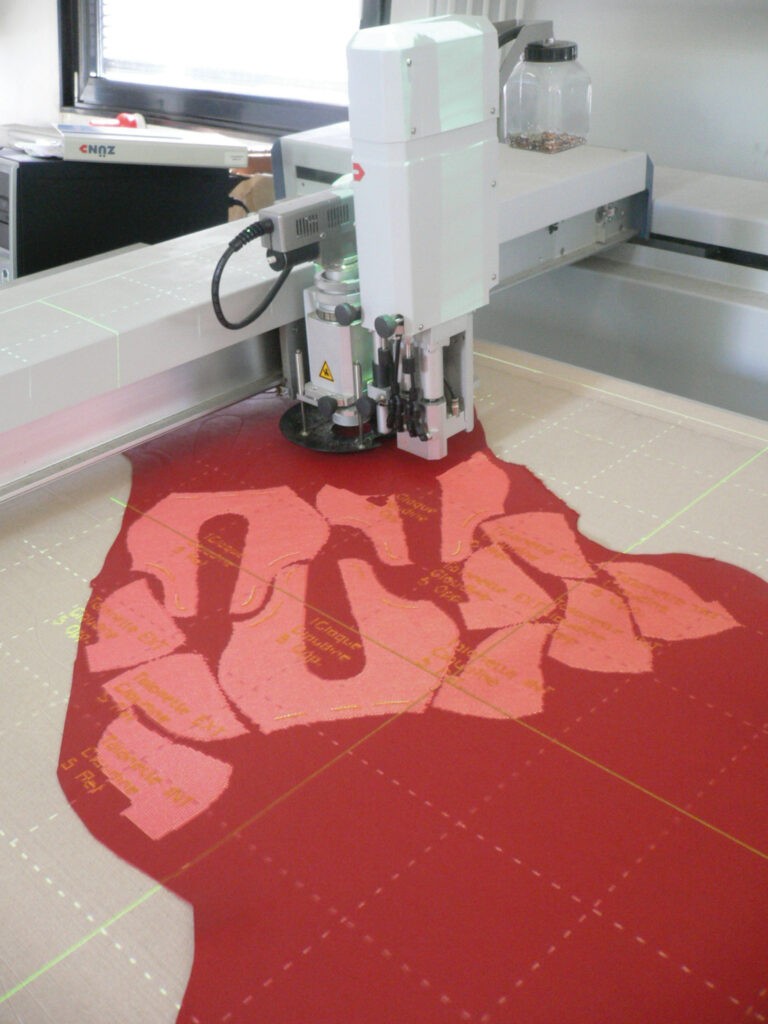